In Safe State 1, the robot independently checks whether a safety-critical situation exists. If this is not the case, the Safe State 1 message is reset immediately and the robot continues its task. If a safety-critical situation is detected, a Safe State 2 message is generated.
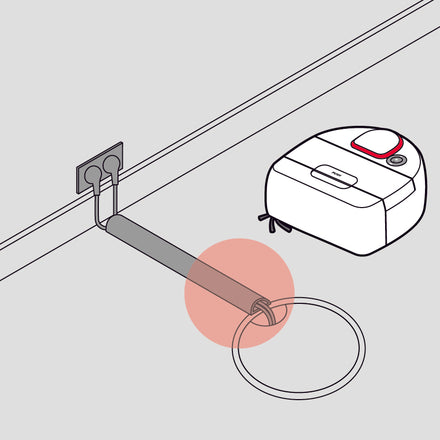
- A responsible person (e.g., facility manager, cleaner) is appointed and trained to oversee the use of the robot vacuum cleaner. They provide on-site support in mapping the cleaning area, ensure a robot-friendly environment, return the robot to the docking station in case of an error, and empty the dust bin regularly.
- The floor area is up to 400 m2 (gross area = total floor area including furniture, obstacles, manually cleaned areas under tables, no-go zones, etc.).
- The robot has a maximum working range of 32 m radius around the docking station.